コアコンピテンシー
フォトリソグラフィ工程
フォトリソグラフィ工程
様々な高速ストリーミングデータ信号が広く使用されているため、より高周波のクロック信号源が必要になります。ただし、従来の機械的方法では、より高い周波数要件を満たすことができなくなりました。このように、フォトリソグラフィーのプロセスを水晶ウェハ業界に適用し、高周波化、小型化、高精度な製品を実現しました。 製造プロセスは以下の通りです。
01
フォトエッチング方式を採用することで、数万枚のブランクをバッチで処理し、ウェハレベルで目標周波数達成を容易にします。
02
上記と同様に、ウェハレベルでは、数万枚のブランクをバッチで処理し、フォトエッチング法にて製品を容易に小型化し、より高い寸法一貫性と精度を実現します。
03
上記と同様に、ウェハレベルでは、同じ方法で回路を処理します。
なぜフォトリソグラフィーなのか?
小型化
(最小サイズ 0806)
半導体プロセスの採用により、お客様の小型化要求に対応。
高周波
(最大500MHz)
3D 構造設計にて、ブランクの剛性を強化し、お客様のニーズに対応。
高精度
(2umの精度)
バッチ生産、正確なサイズ、形状のコントロールにより、電気的及び、品質安定の均一性に対応。
フォトリソグラフィ プロセスは、高周波ブランク設計の技術的限界を克服する。
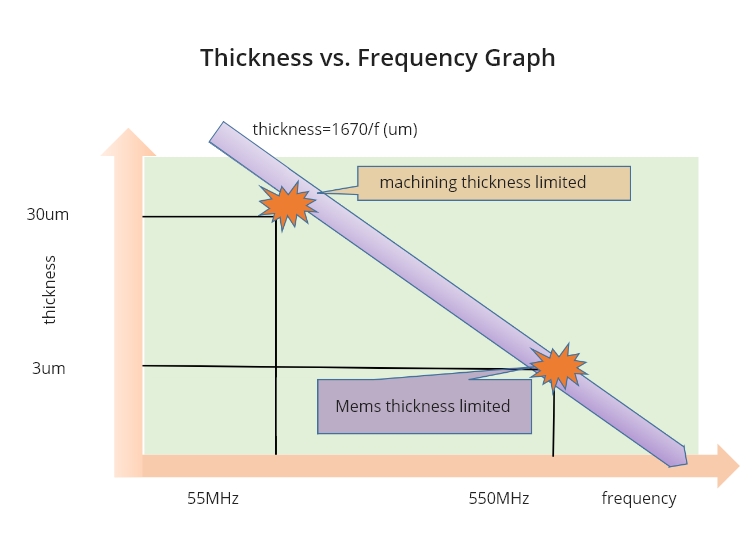
機械的加工プロセスによる水晶ブランクの最薄厚さは約 30um (55MHz) であるため、高周波ブランク (通常は 55MHz 以上) は、技術的な障害を克服するためにフォトエッチングプロセスを使用する必要があります。
* 水晶ブランクの厚さが薄いほど、水晶デバイスの周波数は高くなります。従来のブランクは機械的なプロセス (機械加工) を使用しており、その厚さ限界は、約 30um (55MHz)。
* フォトリソグラフィプロセス技術は、3D 構造設計、ラダー構造、溝構造を可能にし、ブランク剛性強化、厚さ設計の柔軟性向上、製品小型化、より高性能、より高周波数製品の製造を可能にします。
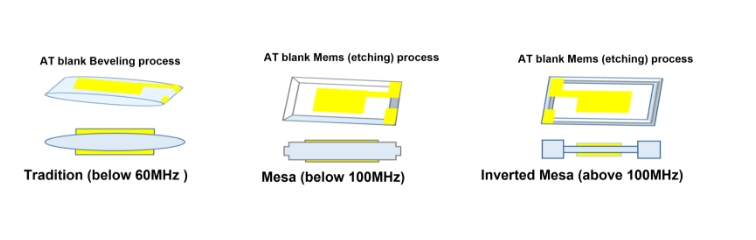
高周波ブランクの厚さは、非常に薄くなり、衝撃による耐久性は非常に弱くなります。
フォトリソグラフィ プロセスは、ブランク構造を3Dラダー構造設計を可能にし、発振領域の厚みは制限されません。そのため、この方法では、次の図が示すように、一般的に 3~30um の厚み達成可能となります。
従来のブランクとフォトリソグラフィ ブランクの比較
品質比較
フォトリソグラフィ プロセスの安定性と精度は、従来のプロセスの安定性と精度よりも大変優れております。
フォトリソグラフィの利点 :
1. バッチ製造、高安定度
2. フォトエッチングプロセスは、小型化、薄化、高精度の要求に対応可能。
従来のプロセス :
1. まず、水晶片ブロックを 2 倍にカットして短冊ブランクにします。
2. 次に短冊ブランクを研磨、面取りし、その後電極形成します。
3. この従来のプロセス (機械加工) では薄化、小型化は、容易ではありません。
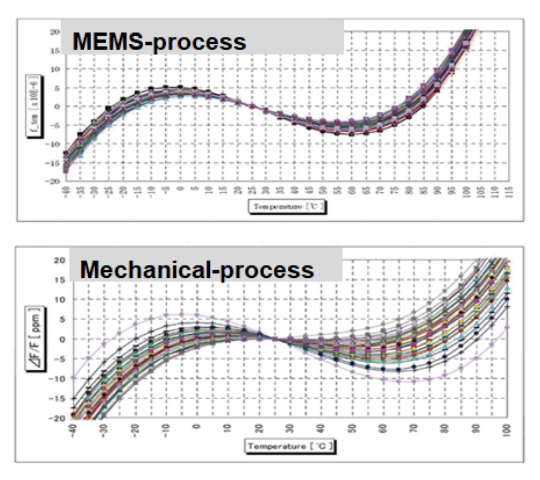
電気的特性の比較
フォトリソグラフィ プロセスの電気的特性は、従来のプロセスよりも優れています (左図参照)。
フォトリソグラフィ (プロセス) で作られた AT ブランクの構造や特徴は次の通りです。
1. 正確なサイズ制御
2. 3D 構造設計
フォトリソグラフィによる各 AT ブランクの特性は、安定した一貫性です。従って、その周波数曲線 (カーブ) は、図で示されている従来のプロセス (機械加工) よりも優れたパフォーマンス (MEMS 加工) を発揮します。
フ ォトリソグラフィ/機械加工製造精度比較
-
サイズ精度1~3μm30~50μm
-
ブランク厚み制限 (精度)3um30um
-
構造3D2D
-
高周波化容易 (Max500MHz)困難 (Max60MHz限界)
-
小型化容易 : パッケージサイズmin 0806(mm)困難
-
安定度より良い悪い